SKALIR Project – Scalable replication of infrared lenses
The use of precise IR optics is often ideal in thermographic applications (e.g. for material analysis or monitoring systems), driver assistance systems and in industrial sensor technology. The exclusion criterion of available IR optics is the usually high costs in conventional production. To open-up new fields of application fields and markets, manufacturers of such systems are searching for economic reasonable solutions. INGENERIC is project partner of the Fraunhofer Institute for Production Technology (IPT) in Aachen and was able to jointly develop a cost-optimized approach to the replicative production of infrared lenses using precision molding of chalcogenide glass.
With this technology, significant savings can be realized by a factor of 5 to 10 in material and unit costs. In isothermal precision molding, glass blanks are heated between two tool halves, formed and cooled in a controlled process. Tested in the visible spectral range and applied industrially, optics can be produced with a wide variety of glass materials and complex geometries, which are used f. ex. in camera lenses, laser or medical technology and components for autonomous driving. The final contours produced in this way exhibit superior properties that cannot be achieved using conventional manufacturing processes such as grinding and polishing.
All started with the scaling of the tooling system
The research project “Scalable molding of lenses for IR applications – SKALIR” was to demonstrate an efficient use of precision molding in the field of infrared optics. First, the Aachen project partners developed an FEM simulation for the scalable forming of chalcogenide glass, which is particularly suitable for high-performance infrared optics and mass markets. The reason for this is that this glass can already be formed at relatively low temperatures with high material efficiency. However, the fundamentally different properties compared to conventional glass had to be explored first. To make precise predictions about the forming process, the material properties were characterized under different conditions. From this, the project partners derived a scalable tool concept with the corresponding mold construction and tool coating. Depending on the target geometry, cost-effective multiple tools are suitable, and wafers can be produced with up to 500 individual IR lenses per pressing process. This replicative approach leads to production scalability and significantly improves the efficiency of the processes compared to the production of lenses with single tools. This creates the prerequisite to access new volume markets for infrared optics.
Background and project partners
The research project “Scalable impression of lenses for IR applications – SKALIR” was funded by the European Regional Development Fund (ERDF) from 01 March 2017 to 29 February 2020. The Fraunhofer Institute for Production Technology (IPT) is consortium leader, participating partners are INGENERIC GmbH and Aixtooling GmbH (which has since merged with INGENERIC GmbH). INGENERIC develops and manufactures optical components for high-power applications as well as optical systems for scientific research, medical and metrological applications and various branches of industry. Founded in 2001 as a spin-off of the Fraunhofer Institute for Production Technology (IPT), INGENERIC today employs around 100 staff members. Since 2013, INGENERIC has been part of the high-tech company TRUMPF.
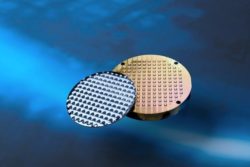
Laboratory samples for the production of infrared optics made of chalcogenide glass on a wafer scale (100 mm) Reference: Fraunhofer IPT
In July 2019, INGENERIC GmbH merged with Aixtooling GmbH, a tool manufacturer for precision optics, thus expanding its manufacturing technologies. Also founded in 2005 as a spin-off of the Fraunhofer Institute for Production Technology (IPT), the company develops and produces high-precision pressing tools for precision molding. In 2019, the headquarters and production facility within the Aachen Technology Region moved to Baesweiler. The expanded competencies and capacities secure the position of the strengthened INGENERIC GmbH as a technology leader with growing future potential.